BATTERIES OF THE FUTURE
The BMZ E.Volution Center develops around 200 new battery systems per year for cars, bicycles, gardening tools, medical devices and other applications.
More than 150 employees in the BMZ E.Volution Center develop all the components of a modern high-performance lithium-ion battery, from concept to series production. In addition to battery cell experts, the E.Volution Center employs designers, hardware and software developers, test engineers and prototype engineers, as well as welding specialists. Thermal management, charging technology and many more innovative topics. Product managers and project managers ensure that the developments are completed in time. From the E.Volution Center, customers receive complete solutions for a wide variety of applications.
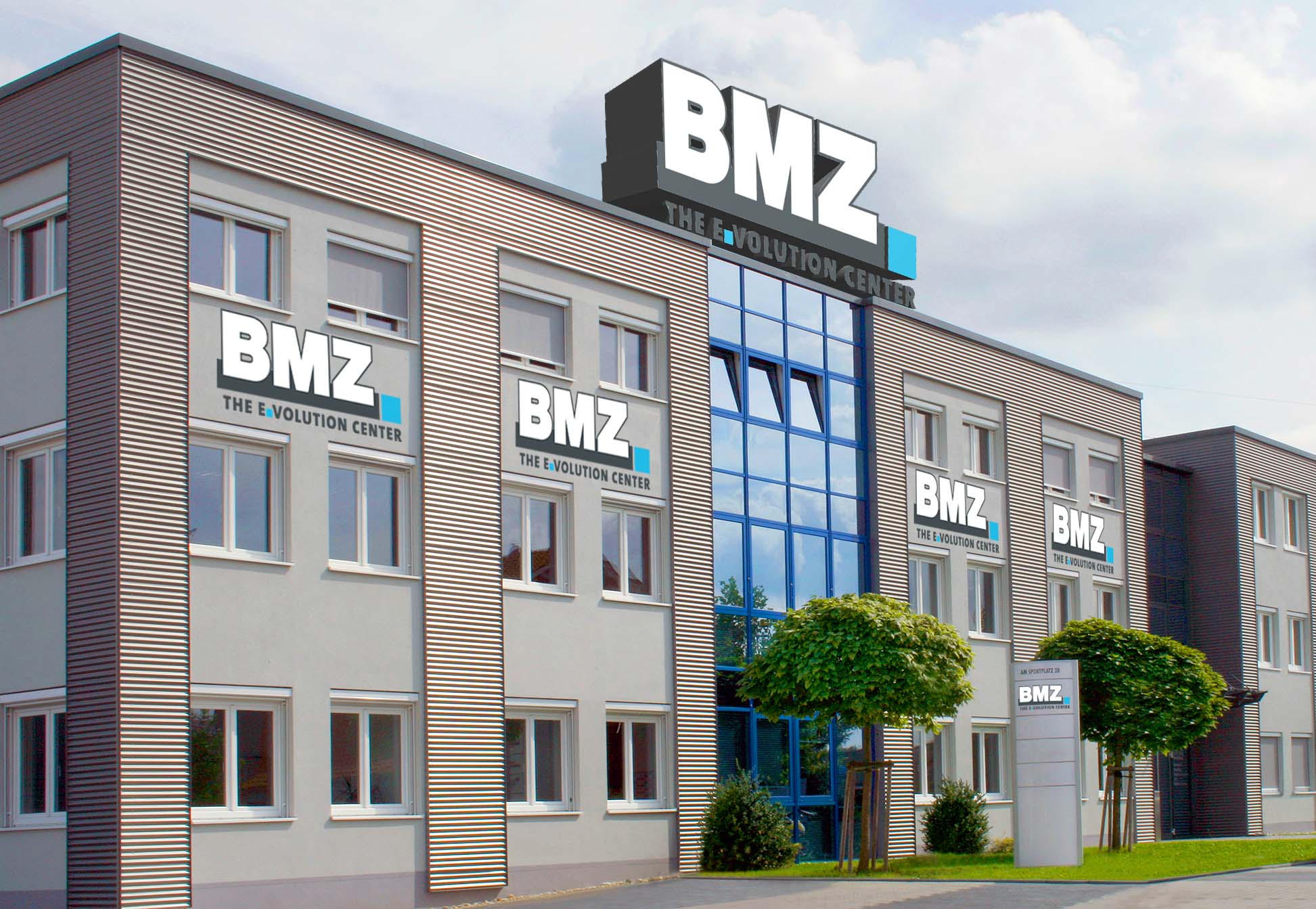
INVESTMENT IN THE FUTURE
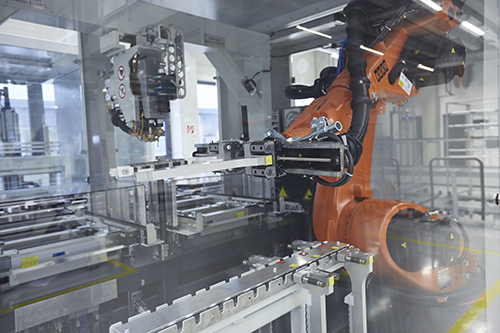
AUTOMATION
Automating the production of lithium-ion batteries paves the way for more productivity, greater process reliability and cost optimization. In the production line, the cells for the batteries are pre-tested. The work steps of welding, soldering and automatic encapsulation are performed automatically by using the welding robot at BMZ.
The soldering machine ensures precise soldering with a stable quality level. The potting system ensures increasing productivity.
Afterwards a final examination takes place. The welding system is used more efficiently by the automated process. This leads to a lower parts per million rate (ppm rate). The abbreviation ppm stands for "parts of a million" and is considered the millionth part of a unit.
LASER WELDING
The welding of round cells has long been one of the core competences of the company. BMZ has extended this with the new technique of laser welding. Thus, the increasing demand for large batteries up to 2.5 tons u. a. for forklifts, cranes and buses in half the time, cost-effective and of high quality. The method is also suitable for the production of smaller battery packs, but require high battery power such. B. in Garden and Powertools or in e-bikes are installed.
The advantages of laser welding are high welding speeds, a high degree of automation, high process reliability and connection quality as well as extremely high dimensional accuracy and slim welds.
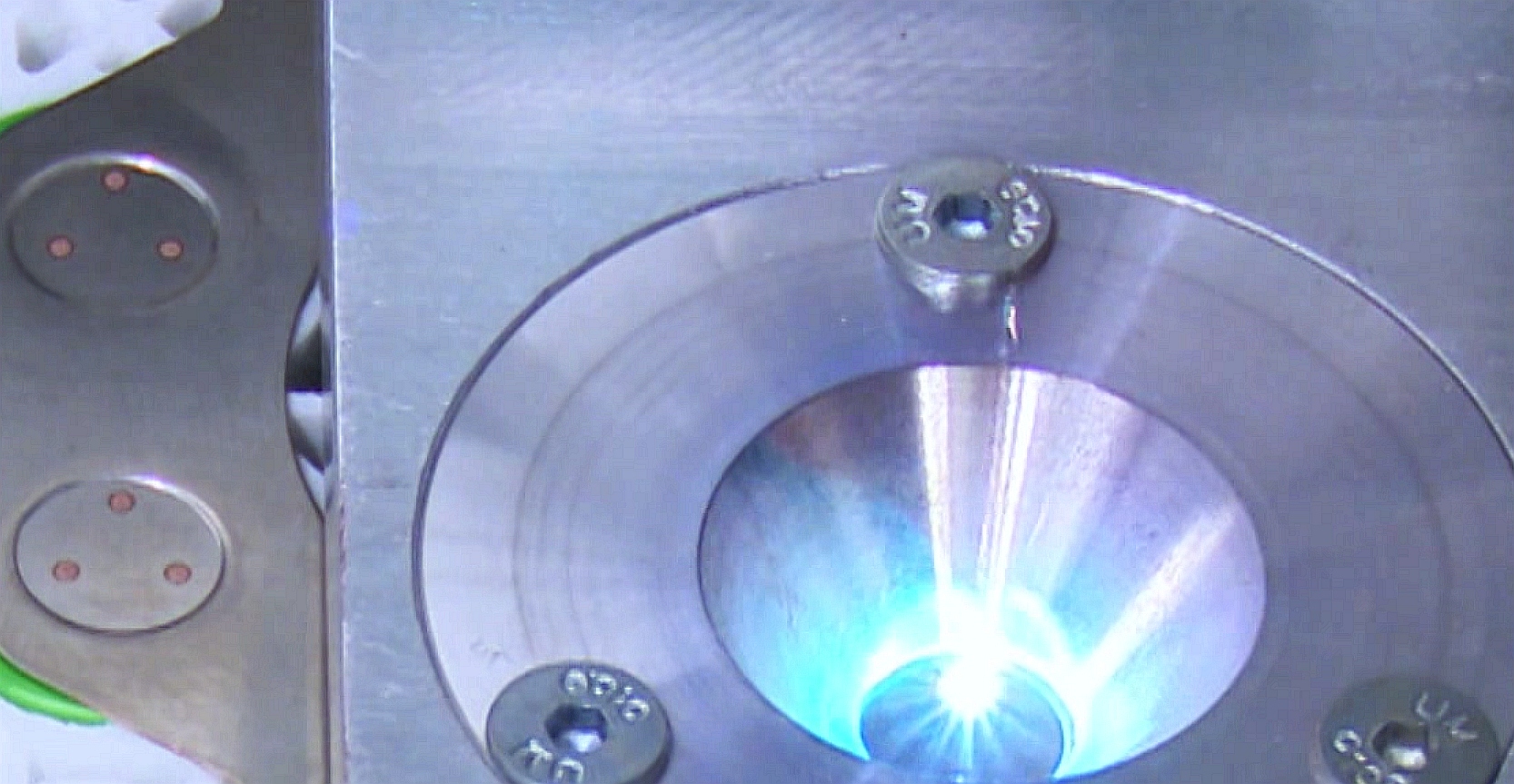
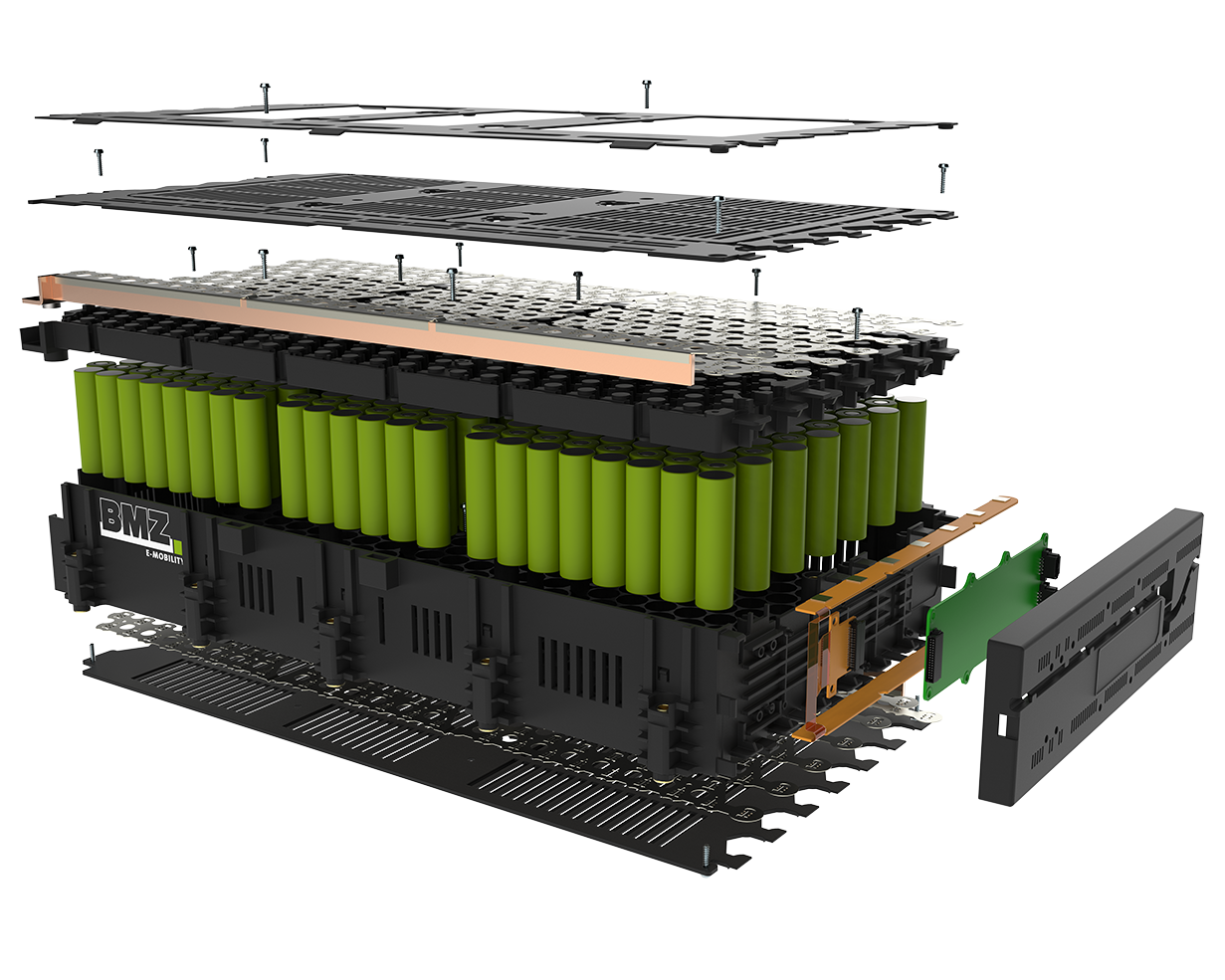